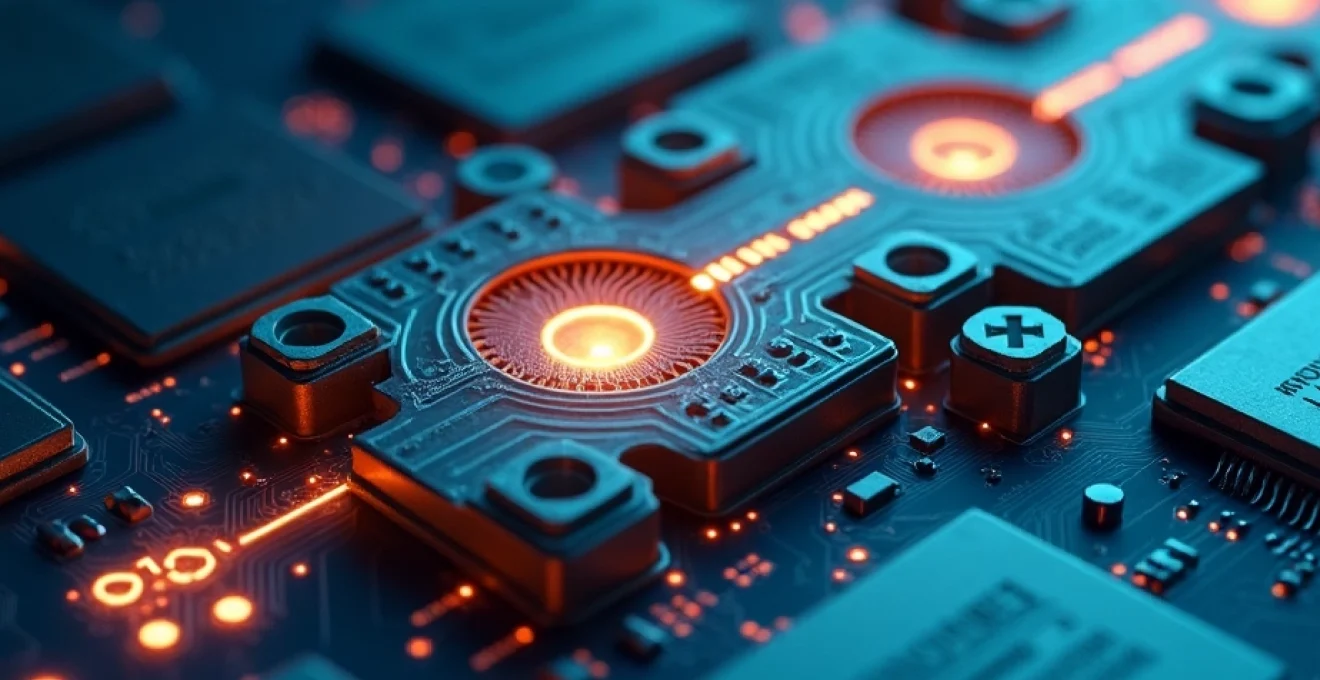
El mantenimiento preventivo se ha convertido en un pilar fundamental para las empresas que buscan optimizar sus operaciones y reducir costos a largo plazo. Esta estrategia proactiva no solo extiende la vida útil de los equipos, sino que también minimiza el riesgo de fallas inesperadas que pueden paralizar la producción. En un mundo donde la eficiencia operativa marca la diferencia entre el éxito y el fracaso, dominar las técnicas de mantenimiento preventivo es esencial para cualquier profesional del sector industrial.
Fundamentos del mantenimiento preventivo en sistemas mecánicos
El mantenimiento preventivo se basa en la premisa de que es más eficiente y económico prevenir problemas que repararlos una vez que ocurren. Este enfoque implica la realización de inspecciones regulares, lubricación, ajustes y reemplazos de componentes antes de que fallen. Para implementar un sistema de mantenimiento preventivo efectivo, es crucial comprender los principios fundamentales que lo rigen.
En primer lugar, es esencial establecer una línea base de rendimiento para cada equipo. Esto permite detectar desviaciones y anticipar posibles fallos. Además, la recopilación y análisis de datos históricos de mantenimiento son fundamentales para identificar patrones y predecir cuándo es probable que ocurran problemas.
Un aspecto clave del mantenimiento preventivo es la estandarización de procesos. Esto asegura que todas las tareas de mantenimiento se realicen de manera consistente, independientemente de quién las ejecute. La creación de procedimientos detallados y listas de verificación es esencial para mantener esta consistencia.
El mantenimiento preventivo no es un gasto, sino una inversión que se paga sola al reducir el tiempo de inactividad y extender la vida útil de los activos.
Otro fundamento crucial es la priorización basada en criticidad. No todos los equipos tienen la misma importancia en el proceso productivo, por lo que es necesario asignar recursos de mantenimiento de manera estratégica, enfocándose en los activos más críticos para la operación.
Planificación estratégica de rutinas de inspección
La planificación estratégica de las rutinas de inspección es el corazón de un programa de mantenimiento preventivo efectivo. Esta planificación implica determinar qué inspeccionar, con qué frecuencia y cómo hacerlo de manera eficiente. Una planificación adecuada no solo asegura que se realicen todas las tareas necesarias, sino que también optimiza el uso de recursos y minimiza las interrupciones en la producción.
Análisis de criticidad de componentes
El análisis de criticidad es una herramienta fundamental para priorizar los esfuerzos de mantenimiento. Este proceso implica evaluar cada componente del sistema en términos de su impacto en la seguridad, la producción y los costos de falla. Los componentes se clasifican según su nivel de criticidad, lo que permite asignar recursos de manera más efectiva.
Para realizar un análisis de criticidad efectivo, se deben considerar factores como:
- Impacto en la seguridad del personal
- Efecto en la calidad del producto
- Costo de reemplazo del componente
- Tiempo de inactividad asociado con la falla
- Frecuencia histórica de fallas
Establecimiento de frecuencias óptimas de revisión
Determinar la frecuencia óptima de las inspecciones es un balance delicado entre prevenir fallas y evitar el mantenimiento excesivo. Las frecuencias de revisión deben basarse en varios factores, incluyendo las recomendaciones del fabricante, el historial de fallas y las condiciones operativas específicas.
Utilizar técnicas de análisis de confiabilidad, como la distribución de Weibull, puede ayudar a predecir con mayor precisión cuándo es probable que ocurran fallas y, por lo tanto, cuándo programar las inspecciones. Es importante revisar y ajustar estas frecuencias regularmente basándose en los datos recopilados durante las inspecciones y el rendimiento del equipo.
Diseño de listas de verificación personalizadas
Las listas de verificación son herramientas esenciales para asegurar que las inspecciones sean completas y consistentes. Deben ser diseñadas específicamente para cada tipo de equipo y deben incluir todos los puntos críticos de inspección. Una lista de verificación bien diseñada guía al técnico a través del proceso de inspección, asegurando que no se omita ningún paso importante.
Al crear listas de verificación, considere incluir:
- Puntos específicos de inspección visual
- Mediciones y lecturas a tomar
- Criterios de aceptación/rechazo claros
- Espacio para comentarios y observaciones
- Acciones de seguimiento requeridas
Implementación de sistemas CMMS para seguimiento
Los sistemas de gestión de mantenimiento computarizado (CMMS, por sus siglas en inglés) son fundamentales para un mantenimiento preventivo eficaz. Estos sistemas permiten programar y hacer seguimiento de las tareas de mantenimiento, gestionar inventarios de repuestos y generar informes detallados sobre el rendimiento del mantenimiento.
Un CMMS bien implementado puede proporcionar beneficios significativos, incluyendo:
- Mejora en la planificación y programación de tareas
- Reducción de tiempo de inactividad no planificado
- Optimización de inventarios de repuestos
- Mejor trazabilidad y cumplimiento normativo
- Análisis de tendencias para mejorar continuamente el programa de mantenimiento
Técnicas avanzadas de diagnóstico predictivo
El mantenimiento predictivo lleva el concepto de prevención un paso más allá, utilizando tecnologías avanzadas para predecir cuándo es probable que ocurra una falla. Estas técnicas permiten intervenir justo antes de que se produzca un problema, maximizando el tiempo de funcionamiento del equipo y minimizando el mantenimiento innecesario.
Análisis de vibraciones con acelerómetros triaxiales
El análisis de vibraciones es una de las técnicas más poderosas para detectar problemas en equipos rotativos. Los acelerómetros triaxiales pueden captar vibraciones en tres dimensiones, proporcionando una imagen completa del estado del equipo. Esta técnica puede identificar problemas como desalineación, desequilibrio, rodamientos defectuosos y resonancia estructural.
Para implementar un programa efectivo de análisis de vibraciones:
- Seleccione los puntos de medición apropiados en cada máquina
- Establezca líneas base de vibración para equipos en buen estado
- Determine límites de alarma para diferentes tipos de fallas
- Realice mediciones regulares y analice tendencias
- Investigue y corrija cualquier desviación significativa
Termografía infrarroja para detección temprana
La termografía infrarroja permite detectar problemas antes de que se vuelvan críticos al identificar puntos calientes anormales en equipos eléctricos y mecánicos. Esta técnica no invasiva puede revelar problemas como conexiones eléctricas sueltas, sobrecarga de circuitos, problemas de aislamiento y fallos en rodamientos.
Para maximizar la efectividad de la termografía infrarroja:
- Utilice cámaras térmicas de alta resolución para obtener imágenes detalladas
- Establezca rutas de inspección que cubran todos los equipos críticos
- Realice inspecciones en condiciones de carga normal para obtener resultados representativos
- Compare las imágenes térmicas con imágenes de referencia para identificar cambios
- Documente y realice seguimiento de todas las anomalías detectadas
Análisis de aceites mediante espectrometría
El análisis de aceites es una herramienta valiosa para evaluar la salud de motores, transmisiones y sistemas hidráulicos. La espectrometría puede detectar la presencia y concentración de partículas metálicas en el aceite, indicando desgaste de componentes específicos. Además, puede identificar contaminantes y degradación del aceite mismo.
Un programa efectivo de análisis de aceites incluye:
- Establecer intervalos de muestreo basados en las recomendaciones del fabricante y las condiciones operativas
- Utilizar técnicas de muestreo consistentes para asegurar resultados precisos
- Analizar tendencias en los resultados a lo largo del tiempo
- Correlacionar los resultados del análisis con otros indicadores de rendimiento del equipo
- Tomar acciones correctivas basadas en los resultados del análisis
Ultrasonido activo para identificación de grietas
El ultrasonido activo es una técnica no destructiva que puede detectar grietas y otros defectos internos en materiales. Es particularmente útil para inspeccionar soldaduras, tuberías y estructuras metálicas. Esta técnica puede identificar problemas que no son visibles en la superficie, permitiendo intervenciones tempranas antes de que ocurran fallas catastróficas.
Para implementar inspecciones por ultrasonido efectivas:
- Seleccione el equipo de ultrasonido adecuado para el tipo de material y la geometría de la pieza
- Capacite a los técnicos en la interpretación correcta de las señales ultrasónicas
- Establezca criterios claros para la evaluación de indicaciones
- Documente y archive los resultados de las inspecciones para análisis futuros
- Integre los hallazgos de las inspecciones por ultrasonido en el plan general de mantenimiento
Gestión de inventarios para mantenimiento eficiente
Una gestión eficaz de inventarios es crucial para un programa de mantenimiento preventivo exitoso. Tener las piezas correctas disponibles cuando se necesitan puede marcar la diferencia entre una reparación rápida y un costoso tiempo de inactividad. Sin embargo, mantener un inventario excesivo puede atar capital innecesariamente y aumentar los costos de almacenamiento.
Para optimizar la gestión de inventarios de mantenimiento:
- Realice un análisis ABC para clasificar los repuestos según su criticidad e impacto financiero
- Implemente un sistema de gestión de inventarios integrado con el CMMS
- Establezca niveles de stock mínimo y máximo basados en el uso histórico y los tiempos de entrega
- Considere acuerdos con proveedores para mantener stock consignado de artículos críticos
- Realice auditorías regulares de inventario para mantener la precisión de los registros
Una gestión de inventarios bien ejecutada puede reducir los costos de mantenimiento hasta en un 30% al tiempo que mejora la disponibilidad de equipos.
Capacitación del personal en nuevas metodologías TPM
El Mantenimiento Productivo Total (TPM) es una metodología que busca maximizar la eficiencia de los equipos involucrando a todo el personal en actividades de mantenimiento. La capacitación efectiva del personal en TPM es esencial para el éxito de cualquier programa de mantenimiento preventivo.
Implementación de pilares TPM en la organización
Los pilares del TPM proporcionan un marco estructurado para mejorar la eficiencia global de los equipos. Implementar estos pilares requiere un enfoque sistemático y un compromiso a largo plazo de toda la organización. Los ocho pilares tradicionales del TPM son:
- Mejoras enfocadas
- Mantenimiento autónomo
- Mantenimiento planificado
- Mantenimiento de calidad
- Educación y entrenamiento
- Seguridad, salud y medio ambiente
- TPM en oficinas
- Gestión de desarrollo
Desarrollo de habilidades de mantenimiento autónomo
El mantenimiento autónomo es un componente clave del TPM que empodera a los operadores para realizar tareas básicas de mantenimiento en sus equipos. Esto no solo reduce la carga de trabajo del personal de mantenimiento especializado, sino que también mejora la detección temprana de problemas.
Para desarrollar habilidades de mantenimiento autónomo efectivas:
- Comience con tareas simples como limpieza e inspección visual
- Proporcione capacitación práctica en lubricación básica y ajustes menores
- Desarrolle listas de verificación claras para las tareas de mantenimiento autónomo
- Establezca un sistema de retroalimentación para que los operadores reporten anomalías
- Reconozca y recompense el buen desempeño en mantenimiento autónomo
Técnicas de resolución de problemas RCA y FMEA
El Análisis de Causa Raíz (RCA) y el Análisis de Modos y Efectos de Falla (FMEA) son herramientas poderosas para mejorar la confiabilidad de los equipos. Estas técnicas ayudan a identificar las causas fundamentales de los problemas y a prevenir su recurrencia.
Para implementar RCA y FMEA efectivamente:
- Capacite al personal en los principios básicos de ambas técnicas
- Utilice un enfoque estructurado para la recopilación y análisis de datos
- Fomente la participación multi disciplinaria en los análisis RCA y FMEA
- Implemente un sistema de seguimiento para asegurar que las acciones correctivas se completen
- Revise y actualice periódicamente los análisis FMEA para mantenerlos relevantes
Análisis costo-beneficio de programas preventivos
Para justificar la inversión en mantenimiento preventivo, es crucial realizar un análisis costo-beneficio detallado. Este análisis no solo ayuda a obtener el apoyo de la dirección, sino que también proporciona una base para la mejora continua del programa.
Cálculo del ROI en iniciativas de mantenimiento
El Retorno de la Inversión (ROI) es una métrica clave para evaluar el éxito de cualquier programa de mantenimiento preventivo. Para calcular el ROI de manera efectiva:
- Identifique todos los costos asociados con la implementación del programa
- Cuantifique los beneficios, incluyendo la reducción de tiempo de inactividad y los costos de reparación evitados
- Utilice la fórmula: ROI = (Beneficios – Costos) / Costos x 100%
- Compare el ROI con otros proyectos de inversión en la empresa
- Revise el ROI periódicamente para asegurar que el programa siga siendo rentable
Evaluación de costos evitados por fallas prevenidas
Los costos evitados son un componente crucial del análisis costo-beneficio, pero a menudo son difíciles de cuantificar. Para evaluar estos costos de manera efectiva:
- Utilice datos históricos de fallas para estimar la frecuencia y el impacto de las averías
- Considere costos directos (repuestos, mano de obra) e indirectos (pérdida de producción, daño a la reputación)
- Implemente un sistema de registro de «casi accidentes» para capturar fallas potenciales evitadas
- Realice análisis de escenarios para estimar el impacto de fallas mayores prevenidas
- Actualice regularmente las estimaciones basándose en los resultados reales del programa
Optimización de ciclos de vida de activos
Un programa de mantenimiento preventivo bien ejecutado puede extender significativamente la vida útil de los activos. Para optimizar los ciclos de vida:
- Establezca una línea base del ciclo de vida esperado para cada activo crítico
- Monitoree el rendimiento y los costos de mantenimiento a lo largo del tiempo
- Utilice análisis de confiabilidad para predecir la vida útil restante de los activos
- Implemente estrategias de mantenimiento adaptadas a cada etapa del ciclo de vida del activo
- Considere el costo total de propiedad al tomar decisiones de reemplazo de activos
La optimización del ciclo de vida de los activos puede reducir el costo total de propiedad hasta en un 20% y extender la vida útil de los equipos en más de un 30%.
El mantenimiento preventivo es una inversión estratégica que, cuando se implementa correctamente, puede proporcionar beneficios significativos en términos de reducción de costos, mejora de la confiabilidad y optimización del rendimiento de los activos. Al adoptar técnicas avanzadas de diagnóstico, implementar metodologías TPM y realizar análisis costo-beneficio rigurosos, las organizaciones pueden transformar su enfoque de mantenimiento de un centro de costos a un impulsor de valor estratégico.